Molten metal atomization is a process that is used to fabricate powders of metals from their melt. In a typical atomizer, the liquid metal is poured down a nozzle into a large chamber while being simultaneously sprayed on by high-pressure jets of water, oil, or gas. This causes the metal droplets to separate and condense into a powder, which collects at the bottom. Atomization has established itself as one of the most popular means for powdering metals. In turn, these powders are crucial to 3D printing metallic parts and in the industrial production of certain compounds that cannot be made any other way.
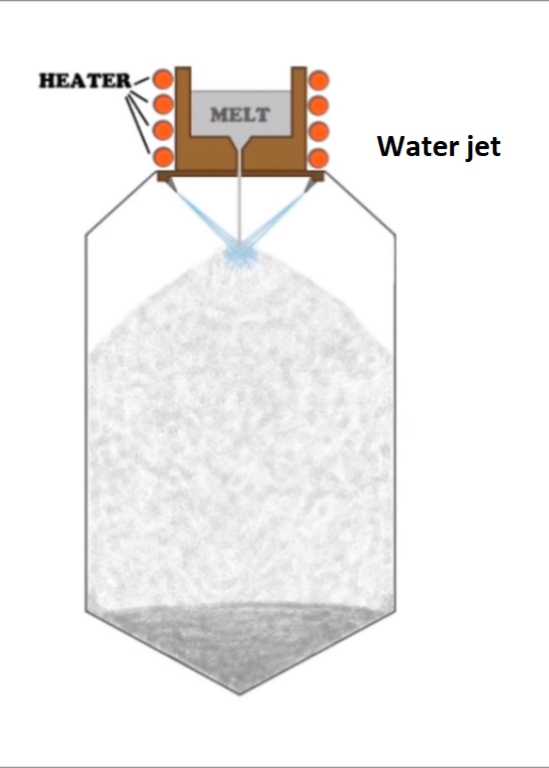
Depending on the nature of the metal and the nozzle, the chamber could either be kept in a high vacuum or in a low-pressure atmosphere. Water is the most common jet material for low reactive metals that melt below 1600 °C. It also has the effect of rapidly quenching the metal once it is broken down into droplets. In fact, the pressure of the water plays a crucial in determining the final size of the particles.
A water jet creates metal particles in four different ways. A water droplet can ‘crater’ the metal stream kicking out a metal drop, it can cause the metal to ‘splash’, it can ‘strip’ a metallic particle from the surface, and finally, it can cause a metal drop to burst into smaller particles. Of the four processes, bursting results in the smallest particle size. In a molten metal atomizer, all four processes happen simultaneously resulting in a heterogeneous microstructure with particles of many shapes and sizes.
Atomization begins at the furnace where the metals are kept liquefied by electrical heating elements. The metal drops into the atomization chamber through the ‘nozzle’ – which is engineered to high perfection and specification. The nozzle is one of the most important parts of the atomization process – a broken or blocked nozzle can result in the metal flow coming to a halt or in increasing the flow substantially – either of which can disrupt the powderization process.
To prevent this, the nozzle must be mechanically strong and provide no resistance to the flow of the liquid metal. At the same time, the nozzle serves as the interface between the hot furnace at the top and the much cooler atomization chamber below. It, therefore, needs to be made of a strong refractory material that is also highly temperature shock resistant.
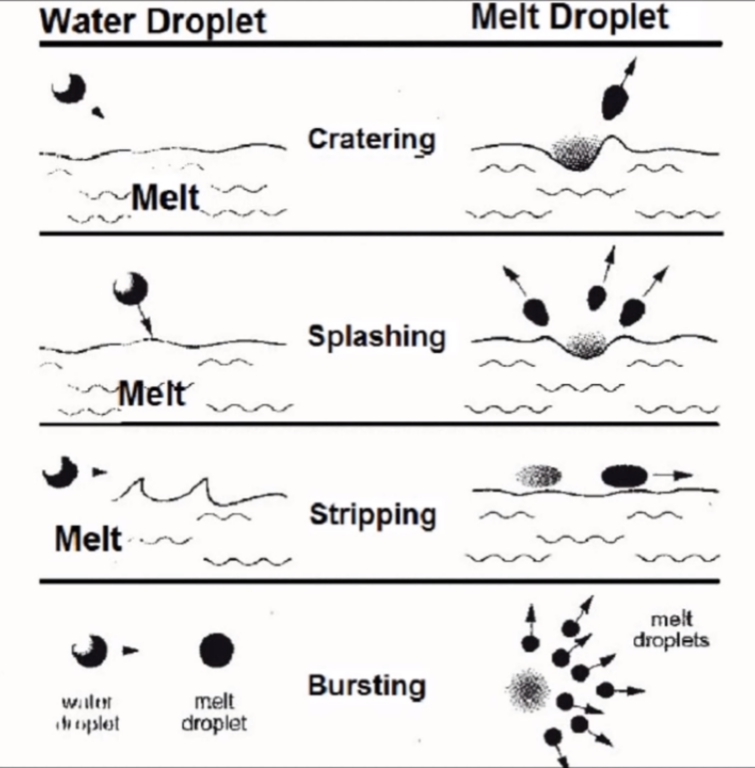
Boron nitride (BN) has come to be recognized as an exceptional nozzle material as it satisfies all these conditions.
It is a ceramic with a high melting point; it is tough enough to prevent cracks; it has high thermal shock resistance; it’s easily machinable. In addition, molten metals cannot ‘wet’ the surface of boron nitride, which means that it is not easily clogged during the atomization process.
The union of these varied properties in one material is remarkable and is in no small part due to boron nitride’s crystal structure.
Like graphite, boron nitride is made from a number of hexagonal layers or ‘flakes’ that are stacked on top of each other. While the bond between boron and nitrogen within each layer is exceptionally strong, the forces that hold the ‘flakes’ together are weak. These individual layers slide on top of each other when acted upon by stresses, making boron nitride an excellent lubricant.
Under high vacuum, boron nitride can survive up to 1800 °C. A gas atmosphere can push this even further to 2100 °C. This means that boron nitride will remain solid through the melting of most metals. The layered graphite structure also imparts it strong thermal heat-conducting and shock resisting properties – the thermal conductivity of BN is 35 W/mK at room temperature.
Boron nitride has a very low thermal expansion. Together with the high heat conductivity, this ensures that the material has very high shock resistance. It can easily withstand the rapid gradations in temperature inside the atomizer. It does not break or crack under thermal stresses.
Boron nitride, however, has higher mechanical durability than graphite. This can be seen in the values of compressive and flexural strength of these materials:
Boron nitride | Graphite | |
Compressive strength | 45 MPa at 20 °C | 17 MPa at 20 °C |
Flexural strength | 18 MPa at 20 °C | 13 MPa at 20 °C |
Boron nitride is therefore capable of withstanding the high mechanical and thermal stresses in an atomizer, without breaking or cracking.
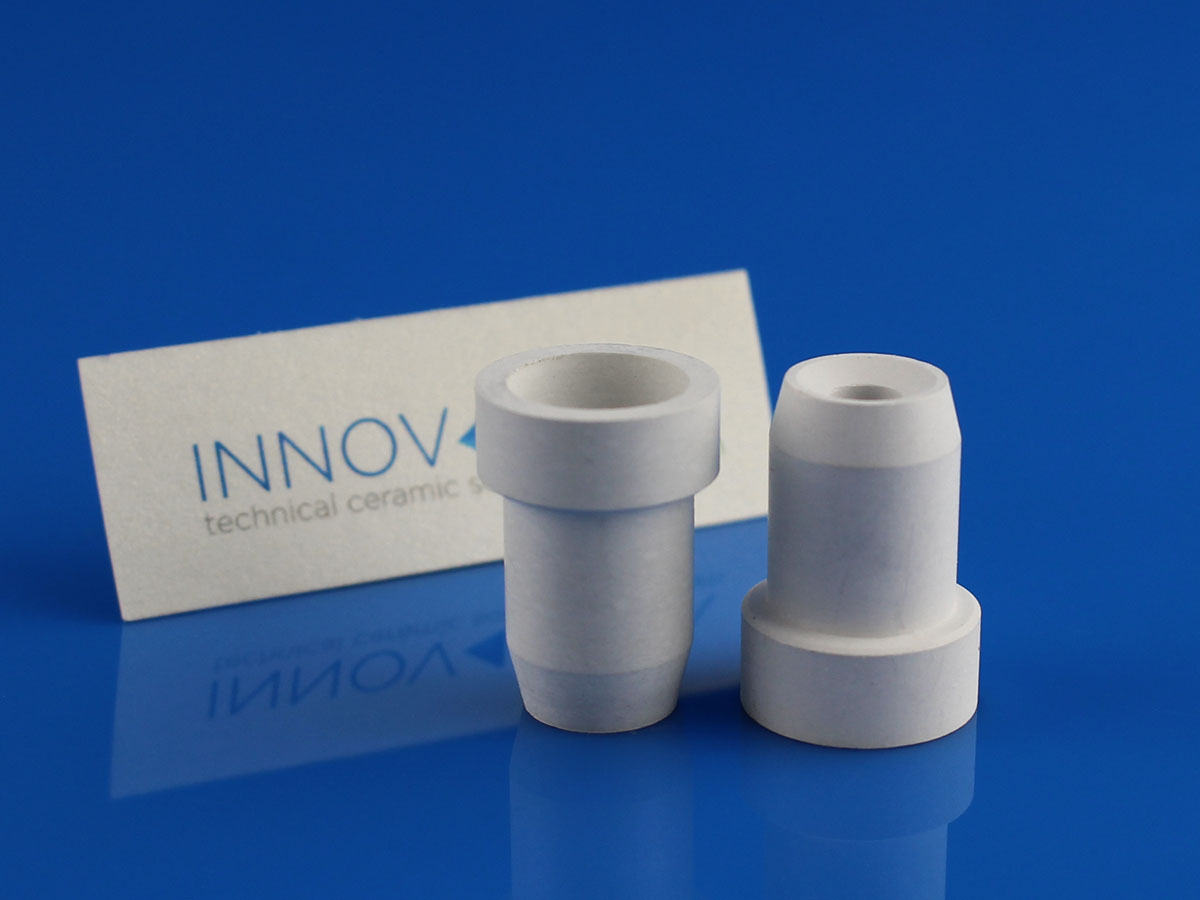
It is also highly machinable, allowing us to craft small threads, holes, and other finer details with high precision and tolerance. Nozzles made from boron nitride can be easily customized, allowing confined as well as free geometries.
In addition, boron nitride cannot be ‘wetted’ by molten metals. This means that a droplet of liquid metals creates an obtuse angle with the BN surface. The surface tension at the droplet-BN interface creates a rolling action, forcing the liquids to slide away. The opposite of this reaction would be a metal drop that sticks to the surface, where it would eventually cool down and block all subsequent metal flow. Thankfully, boron nitride ensures that the atomizer runs smoothly and efficiently.
The boron nitride nozzles from Innovacera are among the best in the industry. They are routinely used for the atomization of gold, silver, platinum, etc. Innovacera allows BN nozzles to be customized for every application while retaining the high thermal conductivity, thermal shock resistance, and non-wettability of the material.
Innovacera is a trusted name in technical ceramics with a large repertoire of boron nitride ceramics. We expertise, along with the enviable properties of BN create the best atomizer nozzles in the industry.
Innovacera is able to supply a wide range of ceramic and boron nitride ceramics as finished components. Our capabilities range from custom-made precision microcomponents with very high tolerance features to large heavy-duty components used in industrial applications. Additionally, standard semi-finished forms such as tubes, rods, bars, plates, crucibles, and spheres are often available from our wide inventory.
Please contact us with full details of your requirements, including drawings where available, and we will review and respond with a quotation as soon as possible.